U.S. Army accelerates the integration of additive manufacturing technologies
The U.S. Army has announced that it accelerates the integration of additive manufacturing technologies to provide Soldiers with cutting-edge munitions.
Additive Manufacturing (AM) is the umbrella term for manufacturing processes that add materials layer by layer to create parts. AM technologies show numerous potentials in terms of rapid prototyping, tooling and direct manufacturing of functional parts and imply revolutionary benefits for the manufacturing industry.
Leaders at the U.S. Army Combat Capabilities Development Command’s Army Research Laboratory designated several research programs as essential for future Army force modernization capabilities. As one of the initiatives, integration of additive manufacturing, also known as 3-D printing, will play a vital role in Army-unique applications.
“Additive manufacturing has opened the door for the creation of geometric designs never thought possible with traditional manufacturing methods,” said Dr. Jason Robinette, program manager of the laboratory’s Science of Additive Manufacturing for Munitions, or SAMM Essential Research Program. “The goal of this program is to take advantage of recent advances in additive manufacturing for developing next generation munitions.”
This program directly supports two of the Army’s modernization priorities, long-range precision fires and next generation combat vehicles. According to Army officials, long-range precision fires aims to neutralize enemy capabilities, while next generation combat vehicles pertains to land superiority in terms of firepower, speed and survivability.
3-D printers build parts in a layer-by-layer fashion and grant Army researchers precise control over the manufacturing process. Compared to the first generation 3-D printers, today’s printers produce large builds in a relatively short amount of time and can incorporate high performance polymers, composites, metals and ceramics as feedstock materials.
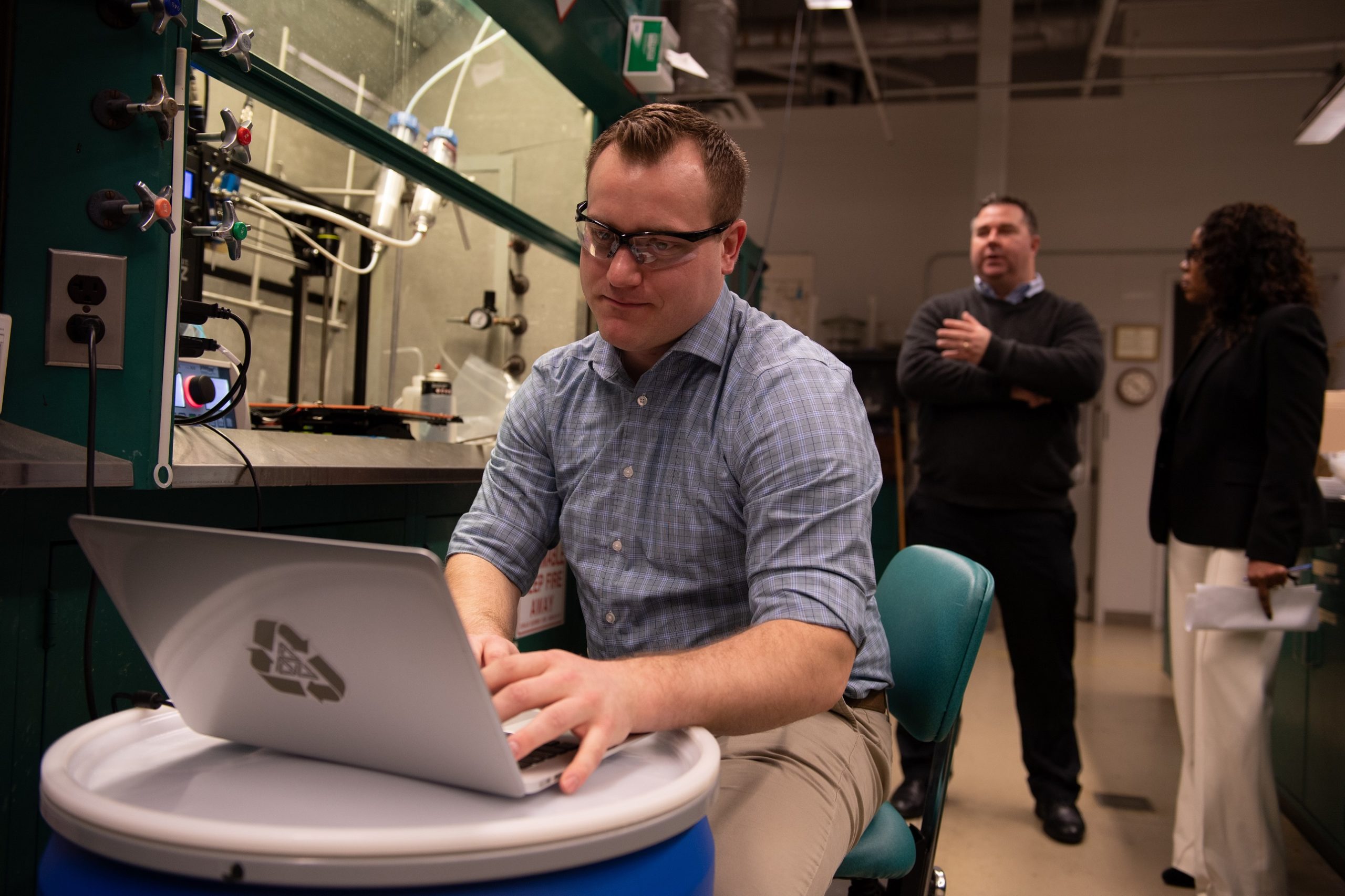
According to Robinette, additive manufacturing has potential to improve the performance of munitions, electronic sensors and fuzes through enhancements of specific production techniques.
Printed gun propellant charges and rocket motors could help achieve higher muzzle velocity and longer range, while better metal feedstocks may increase munition penetration to augment lethality. Researchers said additive manufacturing could even improve the efficiency and durability of electronic sensors and fuzes so they take up less space within the munition and better withstand extreme environments.
“We targeted specific components of the munition that we believe will be most impactful for the Army and has the best potential for transition,” Robinette said.
The research effort consists of three core teams specializing in energetics, metals and hybrid additive manufacturing of munitions technologies, along with a design science team that brings together manufacturing and geometric design to uncover the underlying motive behind each project. In addition, the nature of the research inspires collaboration not just across different divisions and directorates in the laboratory’s Weapons and Materials Research and Sensors and Electronic Devices Directorates, but also with teams in industry, academia and other government agencies.
One of the major goals within this program is to address the issue of how 3-D printed items fail to retain the same mechanical properties as traditionally manufactured parts. Improvements to these features remain a top priority for the team to ensure that 3-D printed parts survive the rough conditions that future munitions will have to withstand.
“We have strategies in place to optimize feedstocks of metals, ceramics, composites and polymers for improved adhesion and microstructure to address these concerns,” Robinette said. “Once those problems are solved, we can start incorporating design tools in such a way to yield never-seen-before geometries for munition components that optimize performance.”
In the short term, the research team plans to first demonstrate the viability of additive manufacturing processes on a component level within the munition. This effort would entail better combustion for propellants, more mass efficient warheads and optimized circuit designs on conformal surfaces. Further down the line, the program intends to demonstrate the integration of different 3-D printing technologies at a system level.
“For instance, we would want to know whether we can print metal casings to help mechanically support rocket motors for high G survivability,” Robinette said. “Can we start printing fuzing schemes to better integrate with explosive charges for increased lethality?”
So far, Army researchers have realized numerous accomplishments in additive manufacturing that promise more exciting developments in the future, Robinette said.
“We’ve printed the highest strength steel in the world in a more cost-effective way while maintaining its properties compared to its cast properties,” Robinette said. “We’ve also printed the world’s first 3-D hybrid microcontroller circuit on a hemisphere that survived high G environments comparable to what is experienced by today’s munitions.”
The team plans to obtain critical design specifications during testing and fine-tune the process to achieve greater performance. Throughout their efforts, the Army modernizations priorities remain at the forefront of their endeavors.
“I think the potential is endless,” Robinette said. “But with this ERP, we’re focused on nearer-term goals to try to deliver a product and capability for the Army that first feeds into its modernization priorities.”
Read More
No comments